Electric motors, pivotal in various applications from industrial machinery to electric vehicles, are subject to different types of noise. These noises not only affect the performance but also the user experience. Understanding, defining, and mitigating these noises are crucial aspects of the motor design phase. Here, we explore the different types of noise in electric motors, their definitions, related keywords, and their association during the design phase.
1. Mechanical Noise
Definition: Mechanical noise in electric motors primarily results from physical components’ interactions, such as bearings, gears, and imbalances in the rotor.
Keywords: Vibration, rotor imbalance, bearing noise, gear noise.
Design Association: During the design phase, careful consideration is given to the selection of bearings, precision in rotor balancing, and the gear design to minimize mechanical noise.
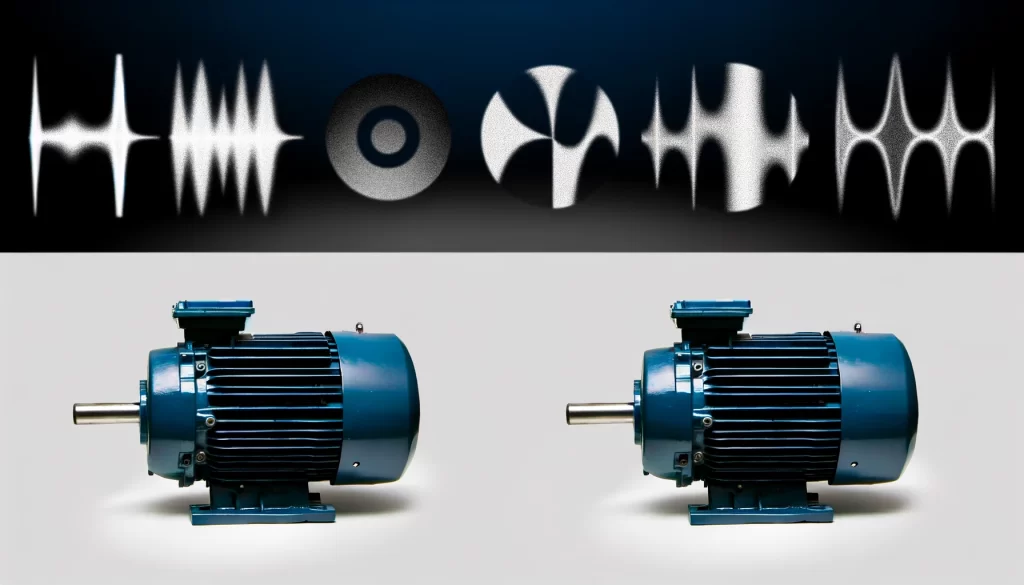
Explanation: Mechanical noise is often characterized by a grinding, knocking, or rattling sound. It results from physical components within the motor, such as bearings or gears, interacting or possibly wearing down. For example, an unbalanced rotor might produce a distinctive rattling or thumping as it spins.
Here are the key findings from recent research:
- Rotor Imbalance: This is a significant source of vibration and noise in electric motors. Imbalance in the rotor leads to uneven distribution of mass, which can cause the motor to vibrate excessively when it rotates. This vibration often results in audible mechanical noise. (source)
- Bearing Noise: Bearings are crucial for smooth operation but can generate noise due to wear and tear, inadequate lubrication, or improper installation. Noise from bearings often presents as grinding or squealing sounds and can vary significantly with the load and speed of the motor. (source)
- Gear Noise: In motors where gears are involved, gear noise can occur due to gear wear, misalignment, or manufacturing defects. This type of noise is generally rhythmic and can be particularly noticeable during speed changes or when under load. (source)
- Vibration Analysis: Techniques such as vibration analysis are essential for identifying and diagnosing sources of mechanical noise. This approach helps in detecting anomalies in the operation of motors, which can be indicative of underlying issues leading to noise. (source)
- Design and Maintenance Strategies: Effective noise reduction strategies include precise engineering designs to minimize component misalignment, the use of sound-dampening materials, regular maintenance to ensure components are in good condition, and using proper lubrication practices. Advanced analytical and numerical methods are used to predict and mitigate these noises, ensuring the development of quieter and more efficient motors. (source)
Understanding these aspects is crucial for diagnosing and mitigating mechanical noise in electric motors, leading to improved reliability and performance.
2. Electromagnetic Noise
Definition: This type of noise is caused by the electromagnetic forces within the motor. It can lead to vibration and noise, especially under load conditions.
Keywords: Magnetostriction, cogging, electromagnetic vibration.
Design Association: Electromagnetic noise is addressed through optimizing magnetic circuit design, selecting appropriate materials, and designing to minimize cogging torque.
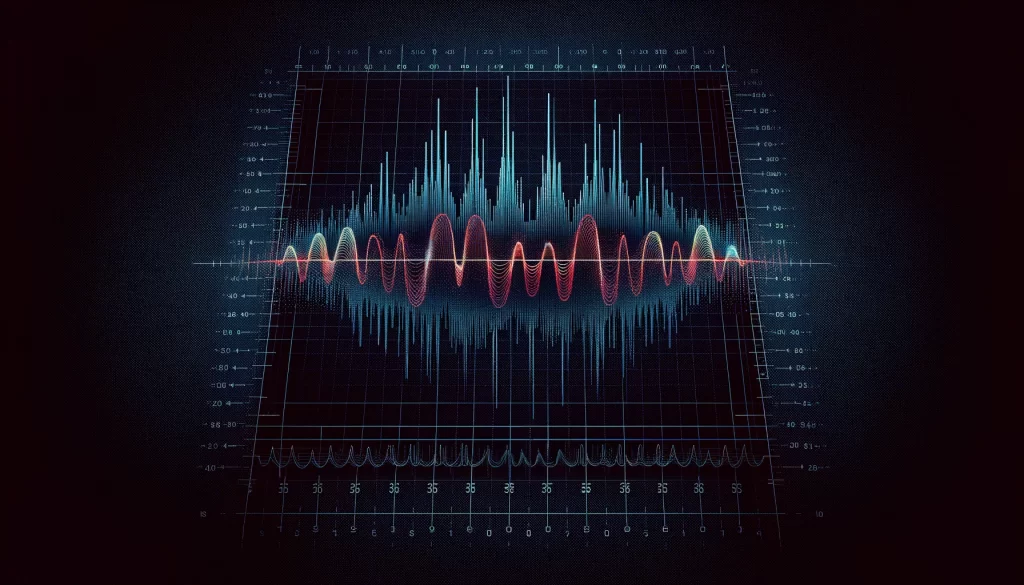
Explanation:
- Noise Characterization and Impact: Electromagnetic noise in electric motors often presents as a high-frequency whining noise, which arises from electromagnetic forces and is further influenced by factors like gear meshing in reducers and pulse width modulation in drive systems. This noise is distinctly different from the low-frequency noise associated with internal combustion engines and is considered particularly annoying due to its high frequency (source).
- Influence of Motor Design: Different motor designs and the physical dimensions of components significantly affect the generation and intensity of electromagnetic noise. For instance, the rotor structure and the air gap between components1 play crucial roles. Optimizations, such as adjusting the air gap or modifying the rotor design, can lead to noticeable reductions in noise levels. For example, a slight increase in the air gap has been shown to reduce noise by about 5 dB (source).
- Noise Reduction Techniques: Various strategies are employed to mitigate electromagnetic noise, including rotor and stator design adjustments like skewing and notching, which help in altering the natural frequencies and reducing the noise intensity. These design changes often come with trade-offs, affecting other motor characteristics like torque and efficiency (source).
- Analytical and Numerical Methods for Noise Prediction: Advanced computational models are used to predict and analyze electromagnetic noise, incorporating methods to calculate electromagnetic forces and the resulting vibrations and noise levels. These models help in understanding how modifications in design influence the noise output and guide the development of quieter motors (source).
These insights suggest that a multi-faceted approach combining advanced design techniques and optimization strategies is essential for effectively reducing electromagnetic noise in electric motors. This holistic view emphasizes not just the need for technical solutions but also a deep understanding of the underlying physical phenomena driving noise generation.
3. Aerodynamic Noise
Definition: Generated by the airflow within and around the motor, particularly in fan-cooled motors or those with significant speed, leading to turbulence and resulting noise.
Keywords: Turbulence, cooling fan noise, air cutting noise.
Design Association: Aerodynamic noise considerations include fan blade design, motor housing shape, and the strategic placement of cooling vents to reduce turbulence and noise.
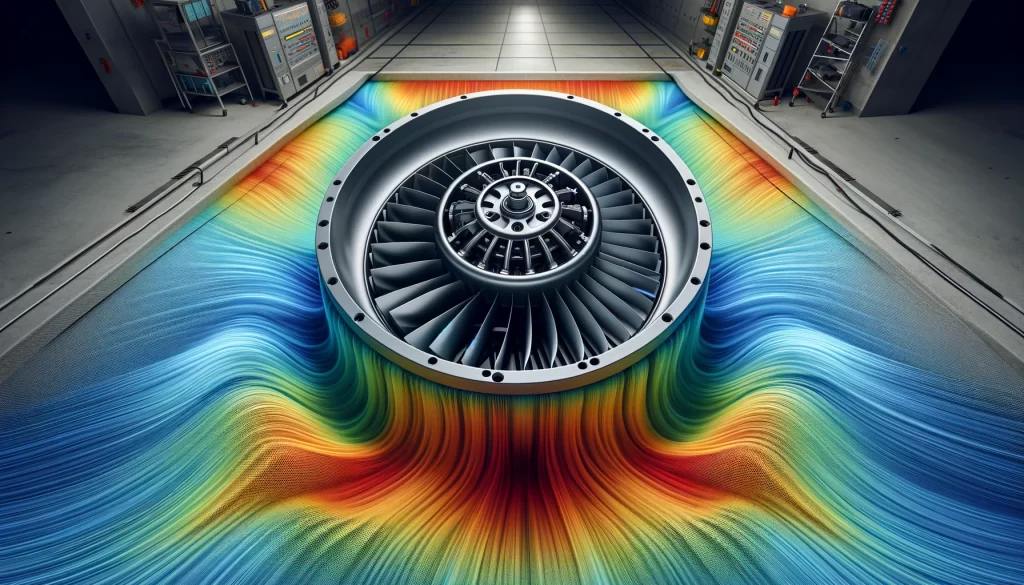
Explanation:
Aerodynamic noise in electric motors is generated by the airflow within and around the motor, particularly noticeable in fan-cooled motors or those operating at high speeds. This noise primarily arises from turbulence created by air moving rapidly around and through the motor’s components. Here are some key insights regarding aerodynamic noise:
- Sources of Aerodynamic Noise: This noise type is chiefly due to the air cutting through the fan blades and the turbulence around the motor housing and cooling vents. These factors cause a whooshing or whirring sound that becomes more pronounced with increasing motor speed. (Source)
- Design Considerations: To minimize aerodynamic noise, special attention is given to the design of fan blades and the shape of the motor housing. Fan blades can be designed to cut through air more smoothly, reducing turbulence. Similarly, the strategic placement and design of cooling vents can help manage air flow to decrease noise levels. (Source)
- Impact of Speed and Load: Aerodynamic noise is particularly noticeable in high-speed applications. The relationship between speed and noise is almost linear, meaning that as motor speed increases, the intensity of aerodynamic noise also increases. This is due to the increased air velocity generating more turbulence around the motor’s components. (Source)
- Mitigation Techniques: Methods to reduce aerodynamic noise include optimizing the fan blade design to minimize turbulence, altering the motor housing shape to streamline air flow, and strategically placing vents to facilitate smoother air passage. These design choices help in achieving more quiet operation while maintaining effective cooling of the motor components. (Source)
Aerodynamic noise, while often less intense than mechanical or electromagnetic noises, can significantly affect the noise profile of electric motors, especially in sensitive applications. Design improvements and strategic engineering are crucial in managing and reducing this type of noise.
4. Electrical Noise
Definition: This noise originates from the electrical switching actions within the motor and its control electronics. It includes both audible noise and electrical interference.
Keywords: Switching frequency, EMI (Electromagnetic Interference), RFI (Radio Frequency Interference).
Design Association: Design strategies involve selecting appropriate switching frequencies, implementing EMI filters, and using shielded cables to minimize electrical noise.
Explanation: Electrical noise often sounds like a high-pitched whine or squeal and is produced by the electrical switching actions within the motor and its control electronics. This noise is more prevalent in motors with rapid switching speed controllers or when the motor operates at high speeds, leading to a frequency that can be audibly discomforting.
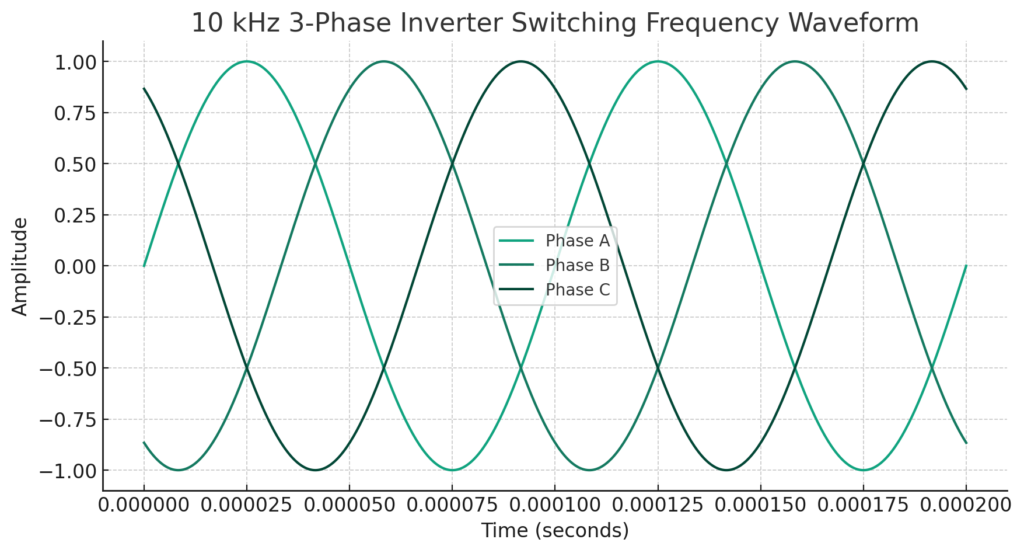
The noise generated from the electrical switching actions within electric motors and their control electronics encompasses both audible noise and electrical interference, such as Electromagnetic Interference (EMI) and Radio Frequency Interference (RFI). Here’s a detailed exploration of these noise types:
- Sources of Noise and Interference: The primary source of this noise is the high-frequency switching of power electronics used to control the motor, such as inverters and converters. These components rapidly switch on and off to regulate the motor’s speed and torque, creating a spectrum of electromagnetic emissions that can manifest as both audible noise and RFI. (source)
- Switching Frequency: The frequency at which the electrical components switch significantly influences the intensity and type of noise and interference produced. Higher switching frequencies often lead to higher-pitched audible noise and can increase the range of RFI emitted. This noise is usually more pronounced in environments with numerous electronic devices or where motors operate at high speeds. (source)
- EMI and RFI: EMI refers to the disturbance generated by an external source that affects an electrical circuit by electromagnetic induction, electrostatic coupling, or conduction. RFI, a subset of EMI, specifically deals with the interference caused by radio frequencies that disrupt the normal operation of electronic devices. Both can affect not only the motor itself but also nearby electronic equipment, leading to a degradation of performance and accuracy (source)
- Mitigation Techniques: Various strategies are employed to reduce both audible noise and EMI/RFI, including designing motor control electronics with proper shielding and filtering techniques. The use of low-impedance paths for grounding, twisted pair cables for wiring, and snubbers to dampen high-frequency oscillations are common approaches. Additionally, careful layout and component selection in motor control circuits can help minimize emissions and reduce susceptibility to interference. (source)
- Impact on Design and Regulation: The need to control EMI and RFI is also a regulatory requirement in many applications, particularly in sensitive environments like healthcare and aerospace, where interference can have critical implications. Engineers must consider these factors in the early stages of motor and electronics design to ensure compliance with international standards for electromagnetic compatibility (EMC). (source)
Addressing the noise and interference from electrical switching is crucial for ensuring the reliability and efficiency of electric motors, particularly in technologically dense or critical environments.
Mitigation Strategies in Design Phase
Mitigating motor noise begins at the design stage, incorporating several strategies:
- Precision Engineering: Ensuring all components are manufactured and assembled to high tolerances to minimize imbalance and misalignment.
- Material Selection: Using materials that reduce magnetostriction effects and selecting bearing types that are quieter and more durable.
- Simulation and Analysis: Employing advanced simulation tools to predict and analyze noise generation, allowing for design optimization before physical prototyping.
- Control Strategies: Implementing advanced motor control strategies, such as Field-Oriented Control (FoC), to reduce torque ripple and associated noise.
- Isolation and Damping: Incorporating vibration isolators and damping materials within the motor assembly to absorb and minimize noise transmission.
Conclusion
Noise in electric motors encompasses mechanical, electromagnetic, aerodynamic, and electrical categories, each with distinct causes and mitigation strategies. By integrating noise reduction measures into the motor design phase, manufacturers can enhance motor performance and user experience. The key lies in a holistic approach, combining precision engineering, material science, advanced simulations, and innovative control techniques to address the multifaceted nature of motor noise.
Understanding and identifying these noises can greatly assist in troubleshooting and improving electric motor designs. Engineers and technicians listen for these specific types of noise during testing and operation to diagnose issues, assess motor health, and implement necessary design adjustments or repairs to minimize noise and enhance motor performance.